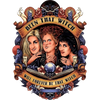
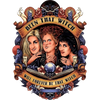
DTF Pressing Instructions: Achieve Perfect Prints
Feb 17, 2024 (Updated on Mar 11, 2025)
If you want to create vibrant and durable designs every time, then you need the right dtf pressing instructions. DTF (Direct to Film) printing is a powerful technique that can elevate your designs to the next level. But without proper guidance, it can also lead to disappointing results. That's why DTF Dallas is here to guide you through all the steps involved in achieving perfect prints using the DTF printing method.
Key Takeaways
- DTF pressing instructions are crucial for creating vibrant and durable prints.
- The DTF printing technique is different from other printing methods, and it's essential to understand its basics.
- Proper preparation of your DTF design, handling the film, and achieving proper registration are important for achieving high-quality prints.
- The right DTF materials can make or break your printing project, so it's important to choose them carefully.
- Proper setup of your heat press machine is necessary for achieving accurate and long-lasting prints.
Understanding DTF Printing
Direct to Film (DTF) printing is an innovative technique that delivers vibrant and long-lasting prints. Understanding the basics of DTF printing is essential for achieving optimal results. Let's explore some of the essential techniques and considerations when using this technique.
The Advantages of DTF Printing
DTF printing offers several advantages over other printing methods. One of the most significant advantages is the ability to print on a wide range of surfaces. DTF printing also offers superior color vibrancy and durability, making it an ideal choice for garments, bags, tags, and other promotional items.
DTF Printing Techniques
The DTF printing process involves several steps, including film preparation, ink application, and heat press transfer. The quality of each process stage directly affects the final print outcome. Therefore, it's essential to use the correct techniques required at each step to achieve optimal results.
DTF Printing Guide
When using DTF printing, it's essential to follow the right technique for your particular project. The DTF printing guide provides valuable tips and tricks for preparing your design, transferring it onto your chosen material, and achieving vibrant and durable prints.
Tip: Always remember to handle the film with care. Avoid scratching or wrinkling the film as it can cause imperfections during the printing process.
Understanding DTF Printing Techniques
There are several DTF printing techniques available for various types of designs and materials. Understanding these techniques is crucial for achieving the perfect print. For example, using a white underbase layer for dark-colored garments can help achieve better print clarity.
DTF Printing Techniques |
Description |
1. Multi-color prints |
Using different colors to create a more visually striking design |
2. Halftones |
Using different sizes and placements of dots to create different tones of the same color |
3. Special effects |
Using DTF printing techniques such as embossing or foil to create a unique design |
By understanding and implementing these essential DTF printing techniques, you can create stunning and eye-catching designs with an impressive lifespan.
Preparing Your DTF Design
If you want to achieve high-quality prints, preparing your DTF design correctly is essential. Below are step-by-step dtf transfer instructions to help you transfer your design onto the film for optimal results:
- Start by cleaning your hands with a lint-free cloth to avoid any oil residue on your prints.
- Print your design onto DTF transfer paper using a compatible printer, such as Epson SureColor F570.
- Before the transfer, allow the ink to dry completely for at least 5-10 minutes to prevent smudging.
- Peel off the transparent backing from the DTF transfer paper and place it on top of the pre-coated white film.
- Use a heat press machine to press the DTF transfer film onto the coated white film with the right temperature and pressure settings. Make sure that you use a teflon sheet over the design to protect it from any direct heat contact.
- Peel the DTF transfer film with the design from the coated white film carefully to prevent any tearing or damage.
- Your DTF design is now ready for heat pressing onto the desired garment or substrate.
Proper handling of the DTF transfer paper and coated white film is crucial to achieve perfect prints. Ensure that you avoid touching them with your fingers as they can absorb oil residues and affect adhesion. Also, keep your printing environment dust-free.
Selecting the Right DTF Materials
To achieve high-quality prints, selecting the appropriate DTF materials is crucial. From films to inks and adhesives, each component plays a significant role in the print outcome. Follow these steps to make the right choices and achieve excellent results.
Different DTF Films
When choosing DTF films, consider the thickness, durability, and adhesion quality. Thin films produce more detailed prints, while thicker ones are more robust. The adhesive quality should have high tackiness to prevent shifting during printing. Matte or gloss finishes are also available to achieve different effects.
DTF Inks
The right DTF ink depends on the type of printer used. Eco-solvent and UV inks are commonly used for DTF printing. However, each has its unique features, advantages, and disadvantages. Eco-solvent ink offers more vivid colors, while UV ink is more durable with better bonding characteristics.
DTF Adhesives
DTF adhesive is essential for proper ink adhesion and transfer on the garment or substrate. The adhesive quality depends on the fabric type, color, and printing method. Clear and white adhesives are available to meet different printing needs.
Preparing Your Heat Press
To achieve the best results with your DTF printing, the proper setup of your heat press machine is critical. Here are some essential DTF heat press tips to help you achieve optimal printing results:
Adjusting the Temperature
The first step in preparing your heat press is to adjust the temperature to the recommended level. Most DTF films require a temperature between 320°F to 340°F, but be sure to check the manufacturer's recommendations for your specific materials. Use a separate thermometer to verify that the heat press temperature matches the settings.
Setting the Pressure
The next step is to set the pressure of the heat press. Make sure to select the right amount of pressure that your design and materials require. Remember, too little pressure results in incomplete transfers, while too much can damage the garment.
Checking the Timing
Proper timing is essential for achieving quality DTF prints. After adjusting the temperature and pressure, it's time to set the timing. Depending on the materials and the heat press used, timings can range from 30 to 60 seconds. Test the timing using a sample piece to determine the right duration.
Using a Teflon Sheet
To prevent any ink smudging and transfer issues, always use a Teflon sheet. Place a sheet on your heat press machine bed and another over the design before the transfer process. This step also helps in improving washability and longevity of the prints.
Preheating the Garment
Before starting the actual pressing process, make sure to preheat the garment for a minimum of 5-10 seconds. This step ensures that the fabric is free from any moisture or wrinkles and allows for proper ink adhesion.
By following these simple yet effective DTF heat press tips, you can achieve optimal printing results and take your DTF printing skills to the next level.
DTF Pressing Techniques
Congratulations! You're now ready to learn the DTF pressing techniques that will bring your designs to life. Follow these steps:
- Preheat your heat press to the optimal temperature, typically around 320°F.
- Spread the garment or substrate on the bottom plate. You can use a Teflon sheet to prevent ink from sticking to the top of the heat press.
- Place your DTF film transfer on top of the garment or substrate, with the printed side facing down.
- Set the heat press for your desired pressure and time settings. Be patient, as waiting too long leads to ink bleeding and not long enough leads to incomplete transfers. The duration and pressure vary by garment and ink type.
- Once the press timer goes off, remove the transfer paper and let it cool down for a few seconds.
- Peel off the transfer paper, and you'll see your design transferred to the garment.
- Done! Celebrate your new skills in DTF pressing.
Remember, the two most important DTF pressing best practices are to find the optimal temperature and pressure settings for each garment type and to test, test, test! Don't rush into a large batch of garments without first checking how your design looks on a test piece.
Troubleshooting Common DTF Pressing Issues
While DTF printing offers many benefits, sometimes things don't go as planned during the pressing process. It's important to know how to troubleshoot common issues so you can achieve the best results possible. Here are some common issues that may arise and solutions on how to fix them:
- Ink bleeding: If you notice the ink bleeding beyond the edges of your design, try adjusting your pressure and time settings on your heat press machine. Also, make sure you're using the right type of film for your design.
- Uneven transfers: This could be caused by improper registration of your design onto the film. Make sure you're following the proper steps for transferring your design and aligning it correctly before pressing.
- Incomplete adhesion: If your design is peeling or flaking off, it could be due to low temperature or pressure settings on your heat press machine. Adjust these settings to ensure proper adhesion of the ink onto the substrate.
By following these dtf pressing instructions, you should be able to resolve most common issues that arise during the pressing process. Remember to experiment with different settings on your heat press machine if necessary, and always use high-quality DTF materials for the best results.
Curing and Aftercare
After successfully pressing your DTF design onto the garment or substrate of your choice, it's time to move on to the final stage of the process: curing and aftercare. This is an essential step for achieving durable and vibrant prints that can withstand multiple washes and maintain their quality over time.
Curing Your DTF Prints
After the pressing is complete, remove the transfer film from the substrate or garment. Then, the print must go through the curing process, which allows the ink to fully set and adhere properly to the surface. Different inks and equipment may require different curing methods, so make sure to follow the manufacturer's recommendations for your specific materials.
Generally, curing is done through the application of heat using a heat press or conveyor dryer. Heat helps the ink to reach optimal adhesion and makes it resistant to abrasion, fading, and cracking, ensuring durability.
Aftercare Instructions
After the pressing and curing process, proper aftercare is essential to maintain the print quality for a longer time. Here are some best practices:
- Wash the garment or substrate inside out with cold water and mild detergent.
- Avoid bleach or fabric softeners.
- Do not iron directly on the print.
- Hang dry or tumble dry on low temperature.
By following these aftercare instructions, the print's longevity can be extended, and its color vibrancy can be maintained for multiple washes.
Now that you have gone through all the steps involved in DTF printing, from preparing the design to curing and aftercare, you can create high-quality prints with confidence. Remember to follow the dtf pressing tutorial and dtf pressing best practices for optimal results. Happy printing!
Advanced DTF Pressing Techniques
Congratulations on mastering the basics of DTF pressing! Now, it's time to explore advanced techniques to create even more eye-catching prints. These dtf pressing best practices will take your designs to the next level.
Multi-Color Prints
One way to elevate your DTF prints is to incorporate multiple colors into your designs. To achieve this, you will need to create a separate film for each color and press them onto the garment or substrate one at a time. Proper alignment is crucial when pressing multiple layers of film, so take your time and use the correct registration techniques. Experiment with different color combinations to create striking designs.
Halftones
Halftones are a technique that uses small dots of varying sizes to create the illusion of shades of colors. This technique can add depth and texture to your designs and is particularly useful when creating prints with photographic elements. Experiment with different dot sizes and frequencies to achieve the desired effect. Remember that halftone dots need to be bigger than the mesh used in screen printing; use finer mesh for detailed prints.
Special Effects
Special effects are a fantastic way to add an extra "wow" factor to your DTF prints. Some of the popular special effects include glitter, puff ink, and metallic finishes. Incorporating these elements will require extra materials and a different pressing process, so make sure you are well prepared before attempting to use them. You can find helpful tutorials and suppliers online or visit DTF Dallas for expert advice.
There you have it, advanced dtf pressing tutorials that will help take your prints to the next level. Remember to keep experimenting and exploring to let your creativity have no limits with the DTF method.
Conclusion
Mastering DTF pressing instructions is key to achieving perfect prints with vibrant colors and durability. By following the step-by-step guide provided in this article, you can enhance your DTF printing skills and ensure customer satisfaction. At DTF Dallas, we specialize in offering expert advice and reliable DTF printing services to ensure that your business achieves nothing but the best possible print outcomes. Whether you're a beginner or advanced DTF printer, always remember to stay updated on the latest techniques and trends to stay ahead of the competition and meet customer demands effectively.
FAQ
Are the DTF pressing instructions suitable for all types of DTF printing machines?
Yes, the DTF pressing instructions provided in this guide are suitable for most types of DTF printing machines available in the market. However, it's always recommended to refer to the manufacturer's instructions for your specific machine to ensure optimal results.
How long should I cure my DTF prints?
The recommended curing time for DTF prints can vary depending on factors such as ink type, fabric type, and heat press settings. As a general guideline, it is recommended to cure DTF prints for around 30 seconds at a temperature of 320°F (160°C). However, we highly recommend conducting a test print and observing the curing process to determine the ideal curing time for your specific setup.
Can I reuse the DTF film after pressing it onto a substrate?
No, the DTF film cannot be reused after it has been pressed onto a substrate. Once the design has been transferred, the film becomes an integral part of the print and cannot be separated without damaging the design. It is recommended to use a new sheet of DTF film for each print job to ensure the best possible results.
How can I prevent ink bleeding during the DTF pressing process?
To prevent ink bleeding during the DTF pressing process, ensure that your design has been properly cured before pressing. Additionally, make sure to use a high-quality adhesive powder that promotes ink fixation and prevents bleed. Proper registration and precise pressure settings on your heat press machine also contribute to minimizing ink bleeding.
Can I use DTF printing for textured fabrics?
DTF printing can be used on textured fabrics, but it may require additional precautions and adjustments. The texture of the fabric can affect the adhesion and transfer of the DTF film. It is recommended to conduct a test print on a small area of the textured fabric to ensure proper adhesion and durability before proceeding with a full-scale print job.
How do I clean DTF residue from my heat press machine?
To clean DTF residue from your heat press machine, it is recommended to use a soft cloth or sponge dampened with a mild detergent or heat press cleaning solution. Gently scrub the affected area to remove any residue. Avoid using harsh chemicals or abrasive materials to prevent damage to the heat press machine.
What types of fabrics work best with DTF printing?
DTF printing can be used on various types of fabrics, including cotton, polyester, blends, and even some synthetic fabrics. However, it is important to note that DTF works best on fabrics with a tight weave and minimal stretch. Fabrics like 100% cotton and cotton-polyester blends tend to yield excellent results, offering vibrant colors and good adhesion.
Can I use DTF printing for dark-colored fabrics?
Yes, DTF printing can be used for dark-colored fabrics. In fact, DTF excels in providing vibrant prints on dark backgrounds. To achieve best results on dark fabrics, it is recommended to use white ink as an underbase layer to enhance the brightness and opacity of the colors. With proper layering and curing, you can achieve impressive results on dark-colored fabrics using DTF printing.
Is DTF printing suitable for large-scale production?
Yes, DTF printing is suitable for large-scale production. With advancements in DTF technology and the availability of high-speed DTF printers, it is now possible to achieve efficient and consistent production of DTF prints. However, it is important to ensure that your workflow, including pre-press and post-press processes, is optimized for large-scale production to achieve maximum efficiency and quality.
Comments 0
Be the first to leave a comment.