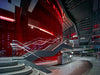
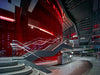
Mastering DTF Printing in Dallas: Perfecting Press Time and Temperature
Sep 16, 2024 (Updated on Feb 10, 2025)
Introduction to DTF Printing
DTF (Direct-to-Film) printing has revolutionized the garment printing industry by offering a cost-effective and versatile solution. Unlike DTG (Direct-to-Garment) printing, DTF printing uses a unique transfer technique that involves printing designs onto a specialized film, followed by transferring them to fabric using a heat press. This method enables:
- Better color vibrancy
- Enhanced durability
- Compatibility with various fabrics
For those seeking premium results, it’s essential to use high-quality DTF supplies and follow the optimal DTF heat press settings guide. Key to ensuring accurate transfers is understanding the correct DTF transfer placement guide and utilizing gang sheets for efficient production. For further assistance, explore our detailed FAQs or contact us directly.
Understanding the Importance of Press Time and Temperature
Press time and temperature are crucial factors in achieving top-notch quality prints with DTF technology. The correct settings are indispensable for transferring designs effectively onto garments. Here’s why:
-
Consistency: Proper press time and temperature ensure consistent prints across multiple garments, which is vital for professional results.
-
Adhesion: Correct settings guarantee that the ink adheres well to the fabric, preventing issues like peeling or fading.
-
Durability: Ensuring the right heat and press time enhances the print’s longevity and washability.
Refer to our [optimal DTF heat press settings guide] for comprehensive resources. Contact us for customized recommendations and DTF supplies.
Optimal Temperature Settings for DTF Printing
Understanding the optimal DTF heat press settings guide is crucial for achieving high-quality prints. Proper temperature settings ensure that the adhesive bonds well without damaging the fabric.
-
Preheat the Press:
- Always preheat the heat press to ensure consistent temperature across the platen.
-
Adhesion Phase:
- Set the press to 300°F (149°C) for 10-15 seconds. This allows the adhesive to bond properly.
-
Curing Phase:
- Use 330°F (166°C) for an additional 10 seconds for optimal curing.
-
Pressure Settings:
- Moderate pressure is ideal. Too much pressure can affect detail and clarity.
For specific queries, refer to FAQs or contact us. Using premium DTF supplies ensures the best results, as detailed in our DTF transfer placement guide.
Determining the Right Press Time
Understanding the key factors influencing press time is essential for achieving superior results in DTF printing. Unlike DTG printing, which involves direct application onto fabrics, DTF requires precise control of press time for optimal ink transfer.
Key considerations include:
- Material Type: Certain fabrics like cotton and polyester have different press time requirements.
- Ink Type: Use ink specified in the optimal dtf heat press settings guide.
- Temperature: Ensure heat-press machines adhere to recommended DTG settings.
For detailed advice on perfecting press time, refer to our premium dtf supplies for quality printing results. Always review gang sheets and dtf transfer placement guides for best practices. For further assistance, visit the FAQs section or contact us.
Common Mistakes and How to Avoid Them
In “Mastering DTF Printing in Dallas,” users often encounter challenges. Missteps can be avoided by understanding and adhering to professional advice.
-
Incorrect Pressure Application
- Over- or under-pressuring during the DTF process.
- Follow the optimal DTF heat press settings guide for correct pressure levels.
-
Inadequate Temperature Control
- Inconsistent or incorrect temperature settings.
- Refer to our premium DTF supplies for quality temperature controls.
-
Improper Transfer Placement
- Misalignment or poor DTF transfer placement.
- Utilize a DTF transfer placement guide for accurate results.
-
Neglecting to Use Gang Sheets
- Inefficient use of materials by ignoring gang sheets.
- Utilize gang sheets to maximize material usage.
For more details, kindly visit our about us page, check our faqs, or contact us.
Tips for Perfecting Your DTF Prints
Optimize Your Heat Press Settings
- Follow the Optimal DTF Heat Press Settings Guide: Adhere strictly to recommended temperature and pressure settings to avoid under or over-curing.
- Run Test Prints: Always run test prints using premium DTF supplies for quality printing results before starting large batches.
DTF Transfer Placement
- Use a DTF Transfer Placement Guide: Ensure accurate placement on garments by following a standardized guide.
- Secure Positioning with Heat-Resistant Tape: Stabilize transfers to prevent shifting during pressing.
Material Compatibility
- Understand DTF vs DTG Printing Key Differences Explained: This ensures you’re using the right method for specific fabric types.
- Select Appropriate Supplies: Utilize DTF-ready-to-press materials from reputable suppliers.
Maintain Your Equipment
- Regular Cleaning and Maintenance: Keep the heat press and printers clean to avoid ink build-up and ensure longevity.
- FAQs and Contact Us Support: Address common issues by reviewing FAQs or reaching out to support for additional help.
Maximize Efficiency
-
Utilize Gang Sheets: Print multiple designs simultaneously on one transfer sheet to save time and resources.
Conclusion: Mastering DTF Printing in Dallas
Mastering DTF printing involves understanding both press time and temperature settings crucial for achieving high-quality results. Leveraging premium DTF supplies and adhering to an optimal DTF heat press settings guide ensures durability and vibrancy in prints. Additionally, comprehending the key differences between DTF vs DTG printing can provide insights into each method’s advantages.
For best outcomes:
- Consult DTF transfer placement guides.
- Utilize gang sheets for efficiency.
- Refer to FAQs or contact us for specialized queries.
By consistently applying these practices, one can ensure DTF projects meet industry standards and client expectations.
Comments 0
Be the first to leave a comment.