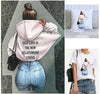
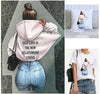
Optimal DTF Heat Press Settings Guide
Mar 21, 2024 (Updated on Sep 1, 2025)
DTF transfers have revolutionized the world of fabric printing, allowing for high-quality designs on a wide range of materials. However, to achieve the best results, it's essential to use the correct heat press settings. Here, we provide a comprehensive guide to help you determine the optimal settings for your DTF heat press.
Key Takeaways:
- DTF transfers require specific temperature settings based on the film and material type.
- For cotton, polyester, and cotton-poly blends, the recommended temperature ranges from 300-375°F.
- When using a heat press, set the temperature between 300-320°F, with a pressing time of 12-15 seconds.
- Handheld presses require a starting temperature of 320°F, increasing gradually if needed.
- Iron temperature for DTF transfers should be adjusted based on the fabric, starting with a lower setting.
Mastering the optimal heat press settings for DTF transfers is crucial for achieving vibrant and durable results. By following the recommended temperature ranges, pressure, and pressing times, you can ensure successful transfers on various fabric types. Let's dive into the intricacies of DTF heat press settings to enhance your printing techniques and produce exceptional designs.
Understanding DTF Film Type and Material Type
Different DTF films and materials have specific temperature requirements to achieve the best results. It is essential to refer to the manufacturer's instructions to determine the appropriate temperature for your specific film type. Additionally, different material types, such as cotton, polyester, and cotton-poly blends, have distinct temperature ranges for optimal adhesion and vibrancy.
Here are the average temperature ranges for pressing different material types:
Material Type |
Temperature Range (°F) |
100% Cotton |
350-375°F |
Polyester |
300-325°F |
Cotton-Poly Blend |
325-350°F |
Ensuring that your temperature settings align with the recommended ranges for both film type and material will help you achieve excellent printing results. It is important to note that variations may exist among different films and materials, so always consult the manufacturer's guidelines for the specific products you are using.
We can see an example of DTF printing on different material types in the image above.
Using a Heat Press for DTF Transfers
When it comes to achieving flawless DTF transfers, using a heat press is a reliable and efficient method. The heat press allows for precise temperature control, ensuring optimal adherence and vibrant designs on various fabrics. To create professional-quality DTF prints, it's crucial to understand the correct heat press settings, pressure, and pressing time.
Firstly, setting the temperature correctly is essential for successful DTF transfers. The recommended temperature range for DTF printing is typically between 300-320°F (149-160°C). This range ensures that the adhesive on the film is activated properly and bonds well with the fabric. Adjust the temperature according to the specific film and material you are using, as different films may have slightly different requirements.
Next, the pressing time plays a crucial role in the transfer process. On average, a pressing time of around 12-15 seconds is suitable for DTF transfers. This duration allows the heat and pressure to activate the adhesive and ensure a secure bond between the film and the fabric. However, depending on the characteristics of the film and material, you may need to adjust the pressing time slightly to achieve the desired results.
Lastly, applying the right amount of pressure is vital for a successful DTF transfer. Medium pressure is generally recommended for most DTF transfers. This level of pressure ensures that the film adheres well to the fabric without causing any damage or distortion. Adjust the pressure according to your specific setup and the manufacturer's recommendations for the transfer film you are using.
Benefits of Using a Heat Press for DTF Transfers:
- Precise temperature control for optimal adhesion
- Consistent and even pressure distribution
- Efficient and fast transfer process
- Ability to handle various fabric types and sizes
- Durable and vibrant results
To summarize, using a heat press for DTF transfers provides excellent control over temperature, pressure, and pressing time, ensuring reliable and professional results. Remember to adjust the temperature, pressure, and pressing time based on the film and material being used. By following these guidelines, you'll be able to create stunning DTF designs that stand out on any fabric.
Aspect |
Heat Press Settings |
Temperature |
300-320°F (149-160°C) |
Pressing Time |
12-15 seconds |
Pressure |
Medium pressure |
Using a Handheld Press for DTF Transfers
If you're using a handheld press for DTF transfers, you have the convenience of portability and maneuverability. However, it's important to note that precise temperature control can be more challenging compared to a heat press. Here are some tips to help you achieve optimal results:
- Start with a lower temperature: Begin by setting the handheld press to a temperature of 320°F. This starting point allows you to gauge the effectiveness of the transfer.
- Gradually increase the temperature if necessary: If the transfer doesn't adhere properly or lacks vibrancy, you may need to increase the temperature. Try raising it by 15 degrees and reapplying the transfer. Continue adjusting the temperature until you achieve the desired result.
- Apply hard pressure: Unlike a heat press that exerts consistent and controlled pressure, a handheld press requires manual force. Apply firm and even pressure to ensure proper adhesion of the transfer to the fabric.
- Press for approximately 20 seconds: Hold the handheld press in place for around 20 seconds to allow the heat to activate the adhesive on the DTF transfer.
Using a handheld press provides flexibility, especially in situations where a traditional heat press may not be practical. However, it's important to remember that temperature control is crucial for successful transfers. With careful adjustment of the handheld press temperature, application of hard pressure, and proper pressing time, you can achieve vibrant and durable DTF transfers.
Using an Iron for DTF Transfers
While using a heat press is recommended for DTF transfers, we understand that not everyone has access to one. Don't worry, you can still achieve good results using a household iron. However, it's crucial to ensure even heat distribution to ensure a successful transfer.
To start, adjust the iron temperature based on the material you're working with. The appropriate iron temperature for DTF transfers will vary depending on the fabric. Begin with a lower setting to prevent scorching or melting of the fabric. It's better to start with less heat and gradually increase if necessary.
If you find that the iron temperature is not hot enough to properly adhere the transfer, gradually increase it towards the cotton/linen setting. This will ensure that the heat is sufficient to activate the adhesive on the film while being cautious not to damage the fabric.
When using an iron for DTF transfers, it's a good practice to use parchment paper or a guard sheet over the transfer. This layer acts as a protective barrier, preventing direct contact between the film and the iron's soleplate. It helps distribute heat evenly and minimizes any potential damage to the transfer or fabric.
Apply hard pressure when pressing the iron onto the transfer. This is important for ensuring proper adhesion between the film and the fabric. Press firmly for about 20 seconds, allowing the heat to activate the adhesive and bond the design to the fabric.
Finally, allow the transfer to cool before peeling. This ensures that the film has properly adhered to the fabric and reduces the risk of peeling or lifting during the process. Once cooled, carefully peel off the parchment paper, revealing your vibrant and durable DTF transfer.
Iron Temperature Recommendations
Material Type |
Iron Temperature Setting |
Cotton |
Low to Medium-Low |
Polyester |
Low to Medium-Low |
Cotton-Poly Blend |
Low to Medium-Low |
Determining Transfer Time and Peel Time
When it comes to DTF transfers, the transfer time and peel time play a crucial role in achieving the best results. These factors may vary depending on your equipment and the materials you're working with. To optimize your DTF transfer time and peel time, it's essential to conduct tests on scrap fabric.
During the testing process, pay attention to the transfer time, which refers to the duration needed to apply heat and pressure for the design to adhere to the fabric. The optimal transfer time can range from 20 seconds to 60 seconds or even longer, depending on factors such as the film type, fabric type, and heat press setup.
After transferring the design, it's important to ensure that the transfer is cool to the touch before attempting to peel it. This allows the adhesive to fully bond with the fabric and ensures a successful transfer. Peeling too early may result in the design not adhering properly or parts of it being left behind on the carrier sheet.
It's worth noting that different film types may have specific peel time requirements. Some films may require immediate peeling after cooling, while others may need a longer resting period before peeling. To determine the correct peel time, refer to the manufacturer's guidelines for the specific film you're using.
Regularly conducting tests and fine-tuning your transfer time and peel time will help you optimize the quality and durability of your DTF prints, ensuring vibrant and long-lasting designs.
Benefits of Optimizing DTF Transfer Time and Peel Time
- Enhanced Adhesion: By finding the optimal transfer time, you can ensure better adhesion between the design and the fabric, resulting in a more durable print that withstands repeated washes and wear.
- Improved Image Quality: Proper transfer time allows the ink to fully cure, resulting in brighter, more vibrant colors and sharper details in the final print.
- Reduced Waste: Fine-tuning your transfer time and peel time minimizes the chances of failed transfers, reducing material waste and increasing overall efficiency.
- Consistency: Optimizing these parameters leads to consistent results, allowing you to reproduce high-quality prints with confidence.
"By conducting careful tests and adjusting your transfer time and peel time, you can unlock the full potential of DTF printing, creating stunning designs that stand the test of time."
Conclusion
Mastering the optimal heat press settings for DTF transfers is crucial for achieving vibrant and durable results. Whether you're using a heat press, handheld press, or iron, following the recommended temperature ranges, pressure, and pressing times will ensure successful transfers. Remember to always refer to the manufacturer's instructions for the specific film type and material you're working with.
With the right settings and techniques, DTF printing can provide fast, versatile, and high-quality custom transfers for various fabric types and products. By understanding the importance of temperature control, pressure application, and precise timing, you can unlock endless possibilities in creating stunning designs on textiles.
Experimenting with different settings and materials will help you find the perfect combination for your desired results. Whether you're a professional printing business, a passionate hobbyist, or a DIY enthusiast, mastering the art of DTF printing will enable you to bring your creative visions to life with exceptional clarity and longevity. So, start exploring the world of DTF printing today and unleash your imagination! And if you have any other questions, our friends at Iris DTF has put together a great DTF Heat Press Guide too, focusing on optimal pressure, temperature & time settings, so don't forget to check that guide too!
FAQ
What are the optimal heat press settings for DTF transfers?
The optimal heat press settings for DTF transfers depend on the film type and material being used. It is important to refer to the manufacturer's instructions for the specific temperature range. Generally, the recommended temperature range for DTF transfers is between 300-320°F. The pressing time should be around 12-15 seconds, and medium pressure should be applied.
How do I determine the temperature for different material types?
Different material types require different temperature ranges for optimal adhesion and vibrancy. For 100% cotton, the temperature should be set between 350-375°F. For polyester, the temperature range is 300-325°F. Cotton-poly blend materials require a temperature range of 325-350°F. It is important to adjust the temperature based on the material being used.
Can I use a handheld press for DTF transfers?
Yes, you can use a handheld press for DTF transfers. Start with a lower temperature, around 320°F, and apply hard pressure for approximately 20 seconds. If the transfer doesn't adhere properly, increase the temperature by 15 degrees and try again. Continue adjusting the temperature until you achieve the desired result. However, it's important to note that precise temperature control can be more challenging with a handheld press compared to a heat press.
Can I use an iron for DTF transfers?
Yes, you can use an iron for DTF transfers. Adjust the iron temperature based on the material you're working with, starting with a lower setting to prevent scorching or melting of the fabric. If the iron temperature is not hot enough, gradually increase it towards the cotton/linen setting. Use parchment paper or a guard sheet over the transfer and press with hard pressure for 20 seconds. Allow the transfer to cool before peeling.
How do I determine the transfer time and peel time for DTF transfers?
The transfer time and peel time can vary based on your equipment and materials. It is recommended to conduct tests on scrap fabric to determine the ideal transfer time for your specific setup. It can range from 20 seconds to 60 seconds or more. After transferring the design, make sure the transfer is cool to the touch before attempting to peel it. Some film types may require different peel times, so always refer to the manufacturer's guidelines for the specific film you're using.
Are heat press settings the same for all DTF transfers?
The heat press settings for DTF transfers may vary depending on the film type, material, and specific equipment being used. It is important to follow the manufacturer's instructions and recommendations for the best results. The temperature, pressing time, and pressure may need to be adjusted based on these factors.
What are the benefits of DTF printing?
DTF printing offers fast, versatile, and high-quality custom transfers for various fabric types and products. It allows for vibrant and durable designs with excellent color saturation and detail. DTF printing also offers the flexibility to print on-demand and in smaller quantities, making it a cost-effective option for both personal and business use.
Comments 0
Be the first to leave a comment.